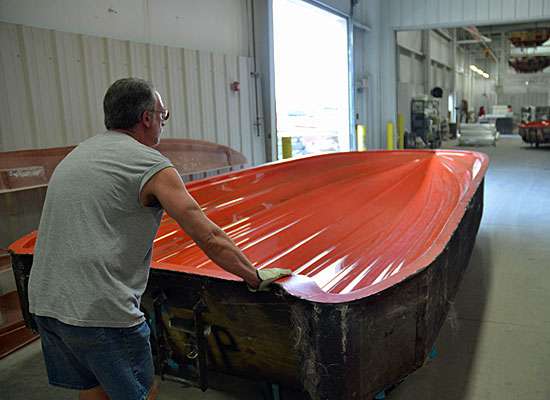
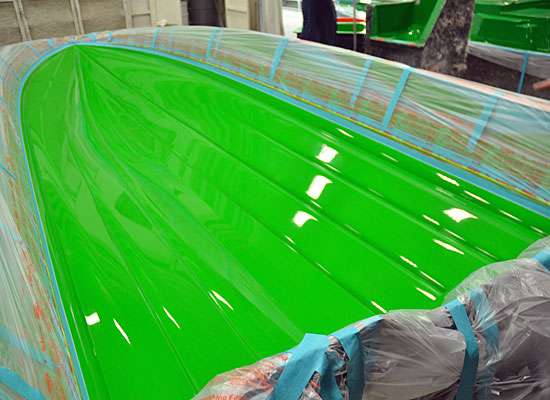
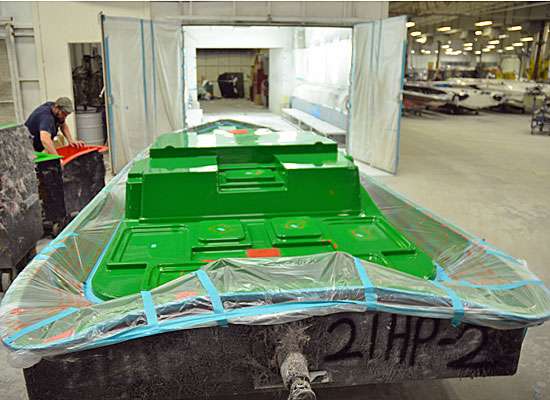
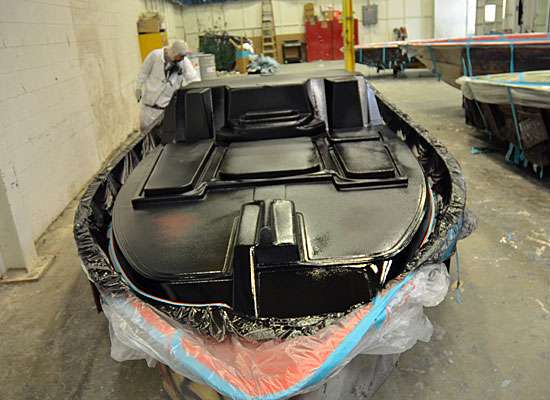
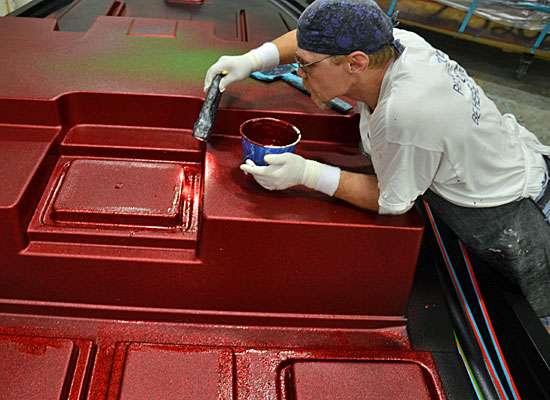
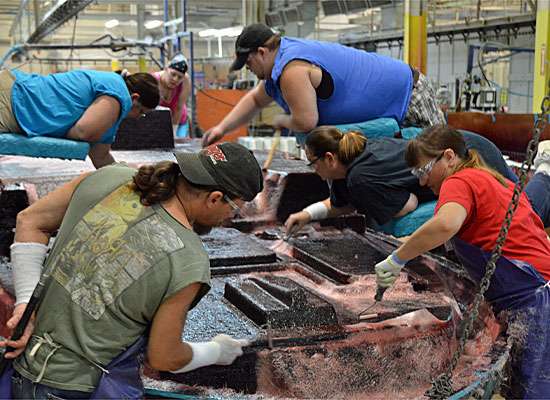
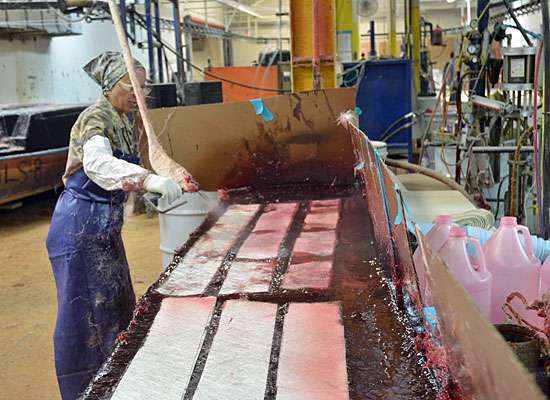
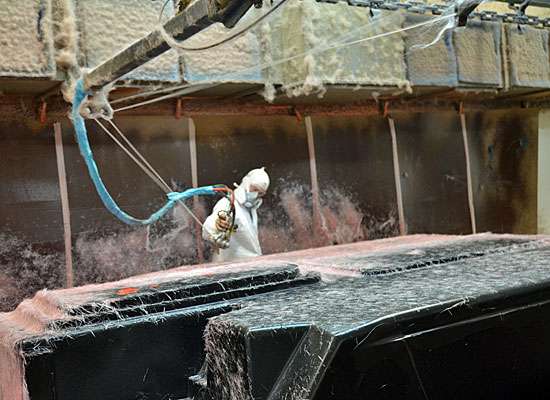
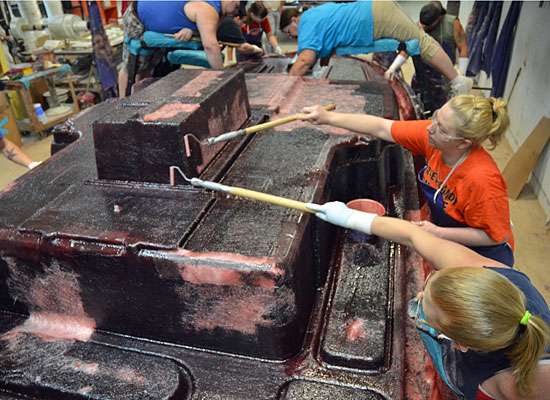
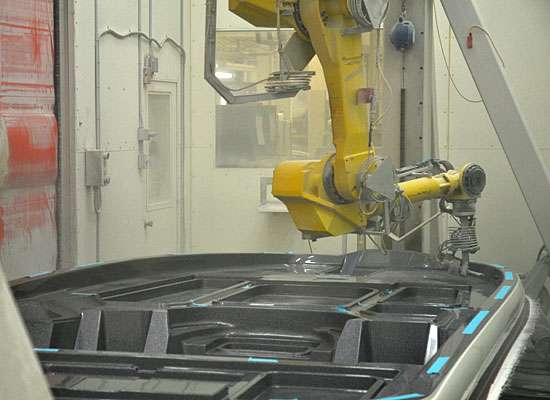
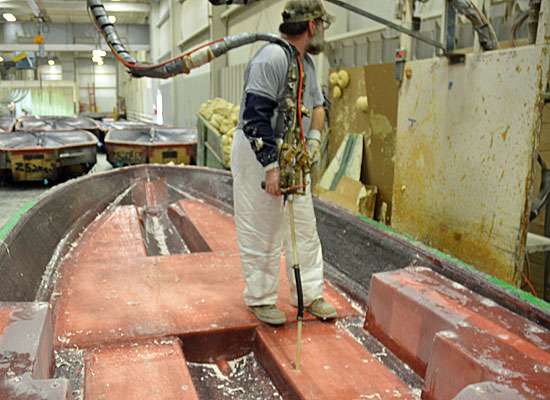
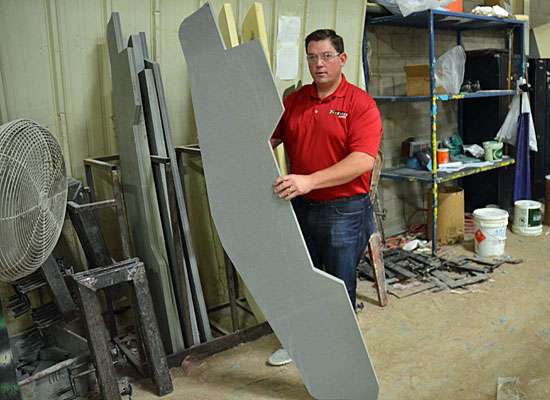
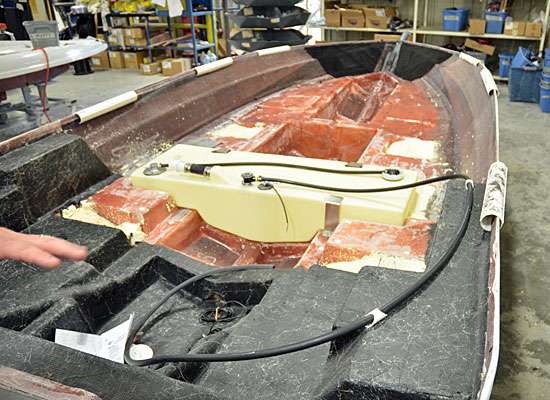
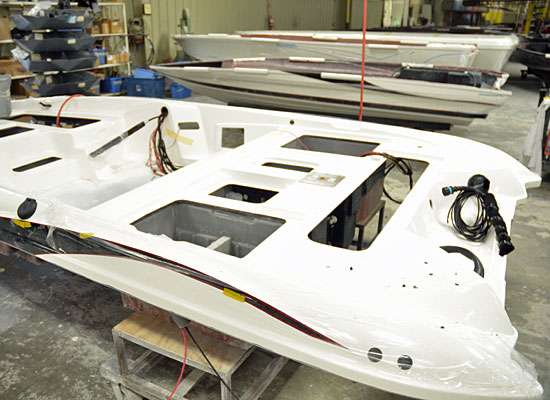
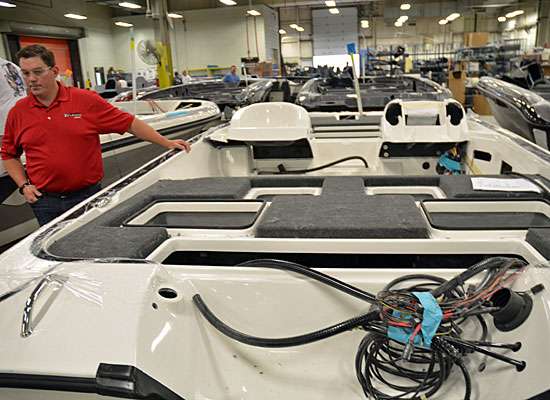
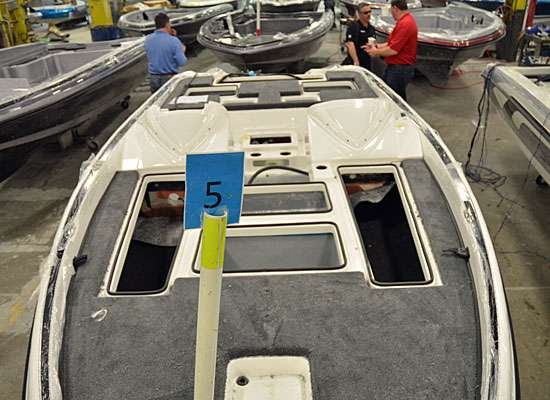
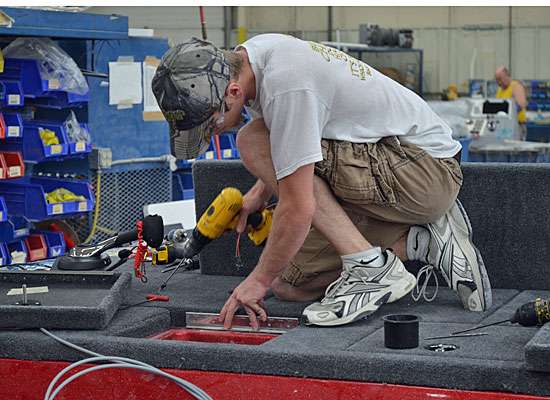
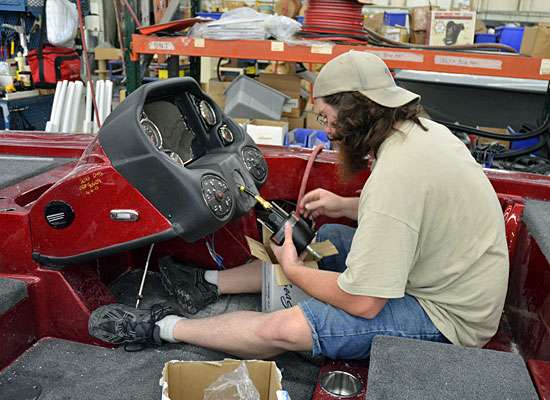
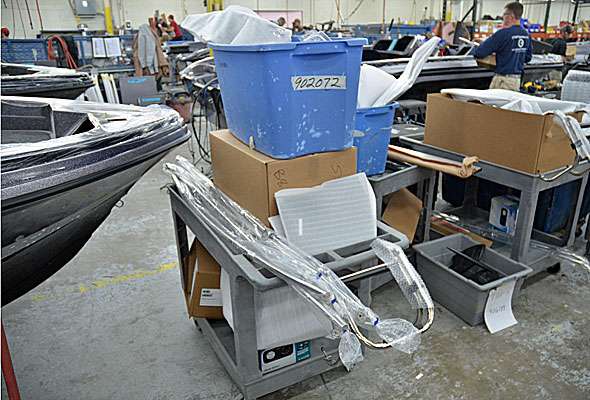
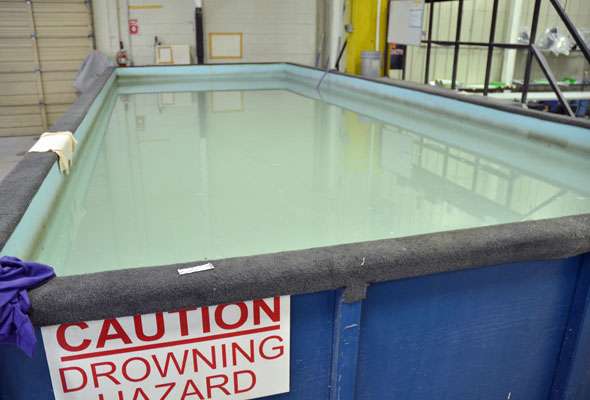
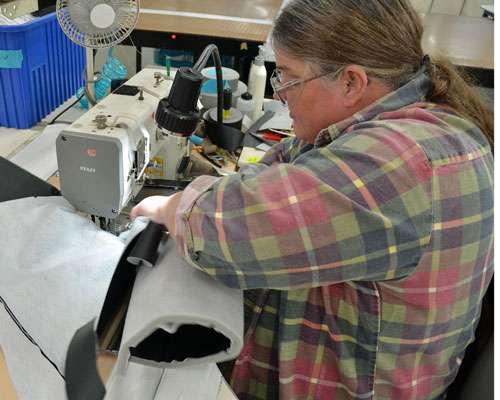
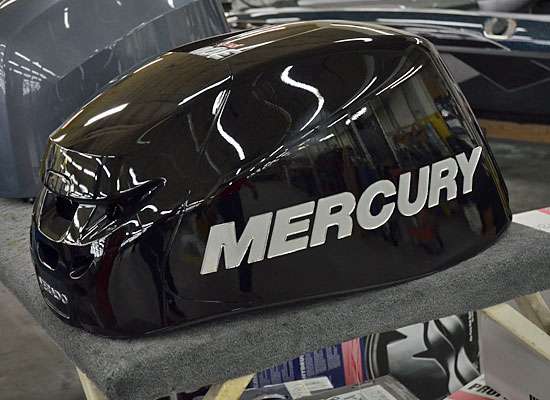
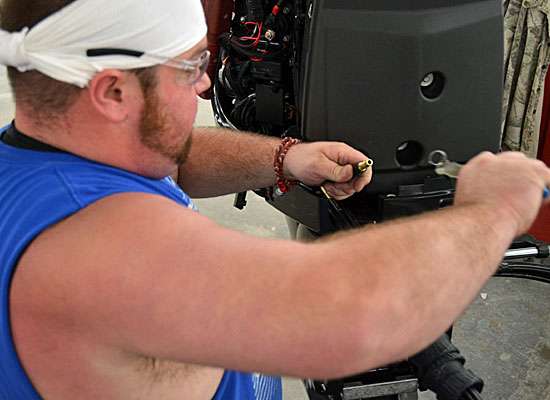
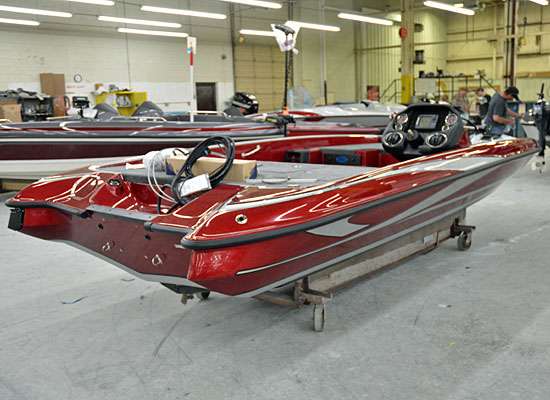
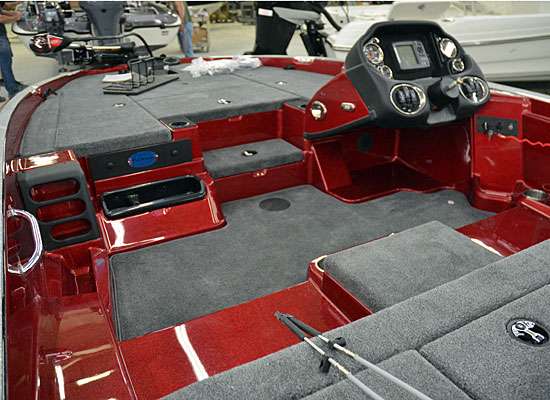
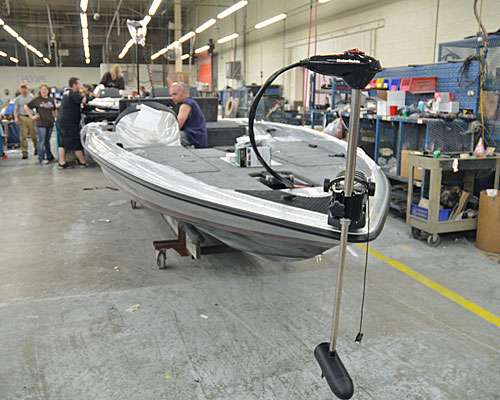
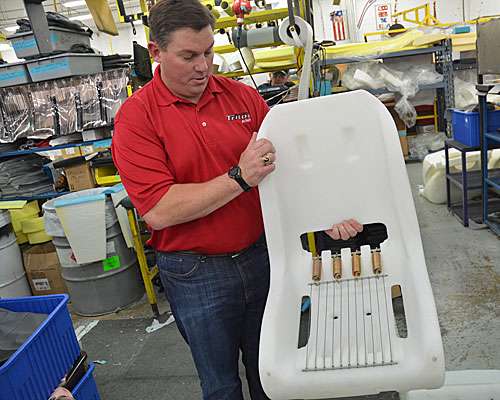
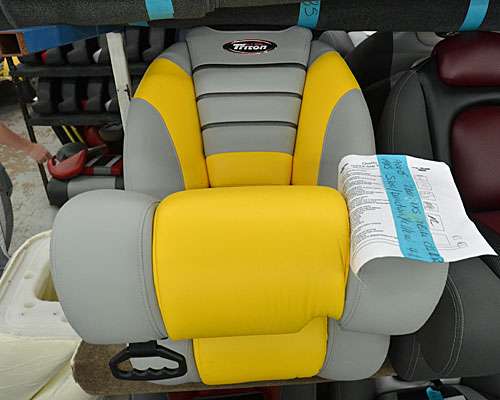
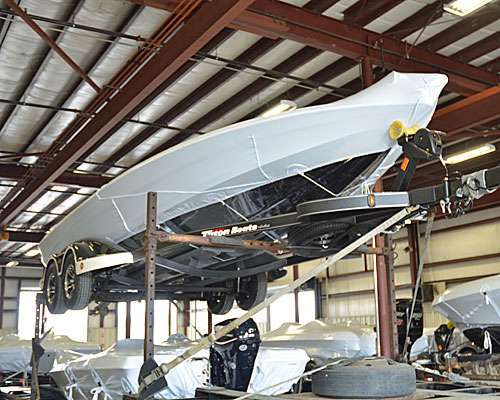
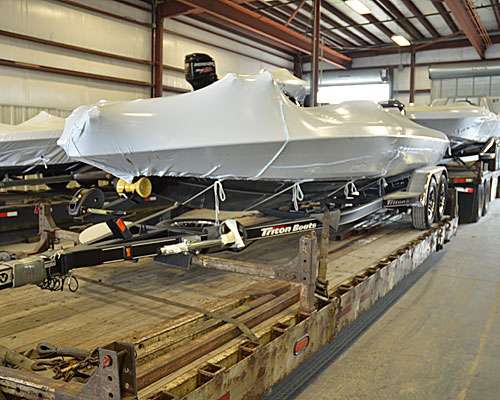
Please enter your details.
We cannot find an active B.A.S.S. Membership for the information you have provided. Please renew your membership here.We cannot find an active B.A.S.S. Membership for the information you have provided. Please try again.Scheduled maintenance. We'll be back shortly. If you continue to have trouble please contact customer service at 877-BASS-USA.
Follow along as we explore the Triton plant in Arkansas and watch as a 21HP is made by hand.