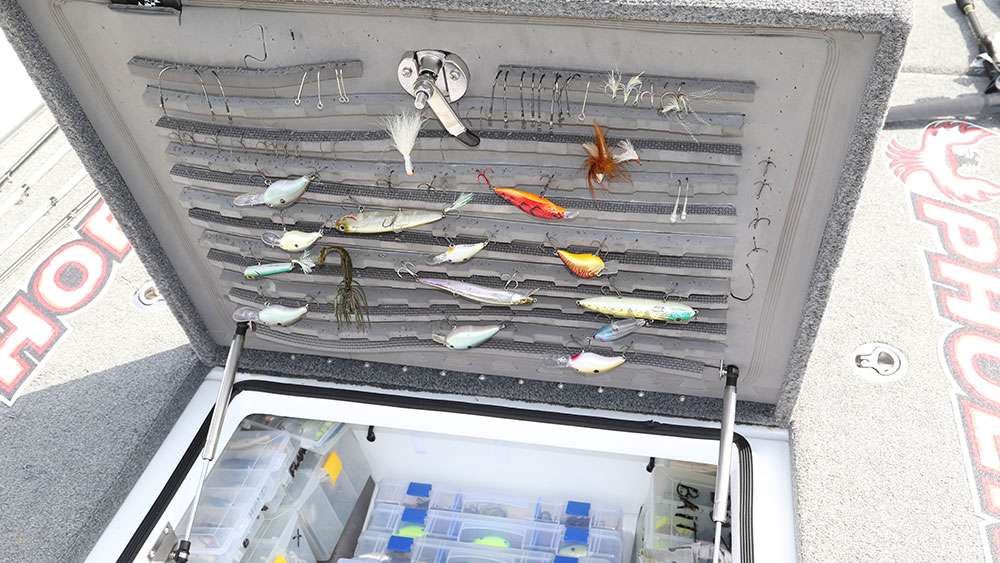
Given his meticulous tackle preparation and legendary precision, it makes sense that Aaron Martens would go to great lengths in protecting the tools of his trade. Funny thing is, one of his primary precautions leverages something so modest that people literally walk all over it.
No kidding; take a close look at — and into — the Alabama Bassmaster Elite Series pro’s boat and you’ll find plenty of the high-density foam made for home gym and playroom flooring. Sold in bundles of interlocking tiles at most home improvement stores, the tough, durable foam repels water so waves and rain won’t risk saturation and ensuing mold.
Martens’ main use, at least in terms of quantity, is the lining he adds to his boat’s storage container lids. Affixing the foam tile to the undersides with professional grade LocTite adhesive provides the insulation he finds critical to protecting his tackle.
“A lot of the lids are made of metal and when you have dark carpeting, they get really warm,” he said. “When it gets really hot, your tackle gets cooked. Your soft plastics will start to break down and separate; they’ll get oily.
“I’ve actually had hard plastics expand and blow up. If you’re fishing in extreme conditions, and you don’t insulate your lids, pretty much everything you own is going to deteriorate faster.”
To that point, Martens also uses foam on rod locker lids.
“The heat can cause your rods to warp or bend, and it can cause the grease in your reels to turn more viscous and drip out. That insulation is just an extra barrier that seems to offer more protection.
“Once, I had a couple of compartments that I didn’t get to finish insulating. The inside temperature difference had to be 20-30 degrees hotter than the ones that I had insulated. You’d reach into one compartment and everything is cool to the touch and you reach into the other one and everything is radiating heat.”
Other foam fixes
Beyond the heat protection, Martens finds several strategic applications for his foam.
Hangin’ out: Cutting strips the width of a lid’s underside creates handy lure hangers with impressive longevity. Dedicating certain strips to treble hook baits, some to spinnerbaits and buzzbaits and others to jigs and single hooks fosters organization and easy access. Maximizing his space, Martens also adds a couple of smaller foam strips to his rod locker lids for handing those “occasional” baits.
“That foam holds really, really well,” he said. “Even after a full year of use, I’ve never had a bait fall out of it.”
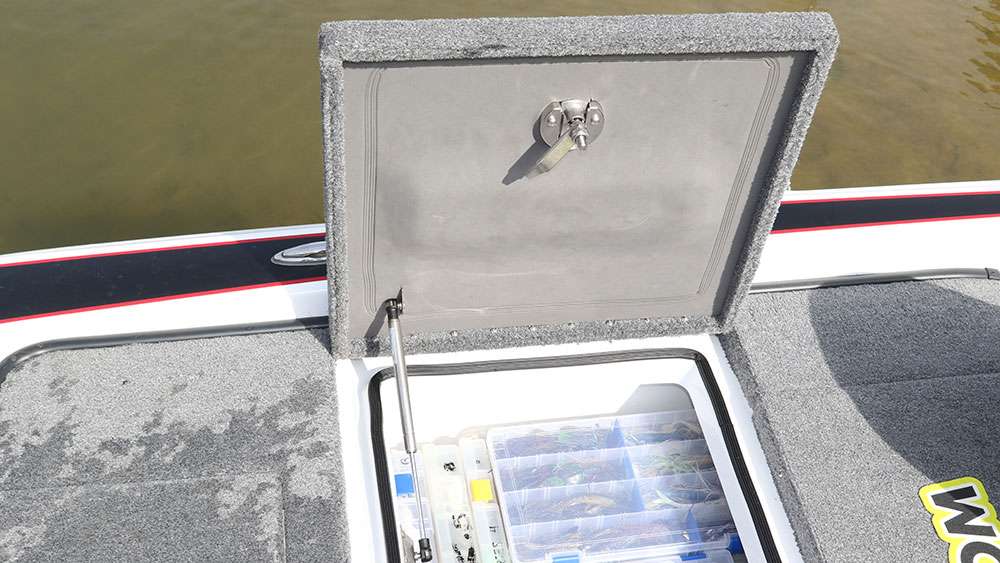
Cushioned and accessible: Snug-fitting foam pieces placed in tackle tray sections keeps loose items like feathered trebles, drop-shot weights, etc., elevated for easy reach while also padding the tackle to prevent damage.
Elevation advantage: Installing foam strips at the bottom of his storage compartments allows clearance for tackle trays in the event of water intrusion.
“This elevates my (tackle containers), so if I do get water in a compartment — maybe you open a lid and a wave splashes into the boat — the water doesn’t get into your (containers),” Martens said.
Additionally, Martens said this padded surface serves as a shock absorber for rough rides. Excessive bouncing and bumping can chip the paint on tungsten weights and various hard baits.
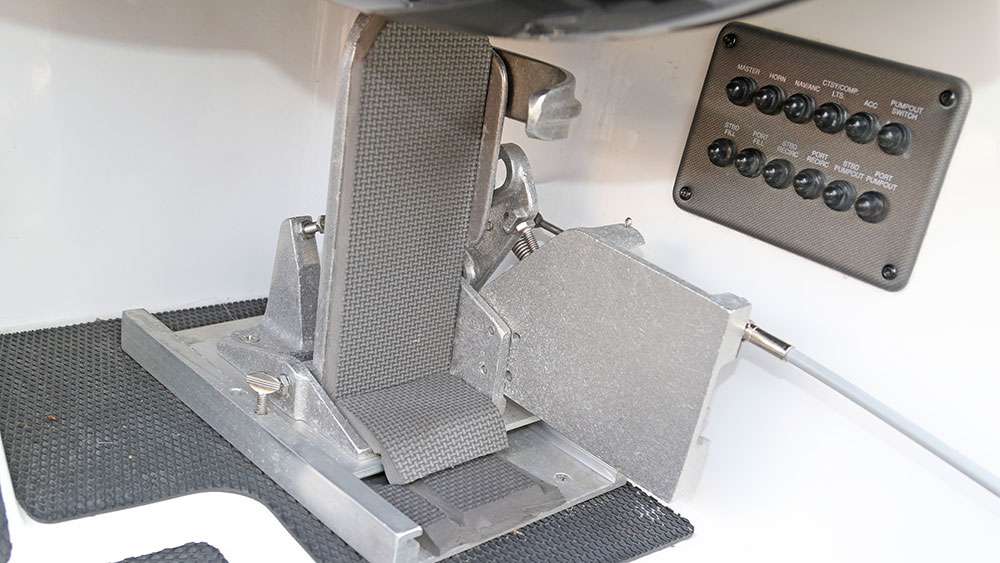
Step to it: Martens fishes barefoot during warmer months, so adding foam to his T-H Marine Hot Foot and his trolling motor pedal ensures tolerable surface temperatures. Even with shoes, he said, the padding improves comfort during long runs. Similarly, Martens keeps a couple of foam squares on his front deck for foot-friendly standing spots.
Take a seat: While sitting and working on tackle, a foam pad makes hard, warm, wet or otherwise uncomfortable surfaces more bearable during the long hours spent prepping his tackle.
Tools and tips
With countless hours invested in the use of high-density foam to accessorize his bass boat, Martens has dialed in several technique points that’ll facilitate the replication of his strategy.
- Having tried scissors, razor blades, box cutters, etc., Martens finds the 3-inch blade of his Kershaw pocketknife most effective for cutting foam. His knife has a partially serrated blade, but he mostly uses the straight edge section, as it yields cleaner lines.

“I’ll use a sharpener on that (straight section) and if I’m going to install foam in my whole boat, I’ll probably sharpen it six times so I keep it like a razor blade,” Martens said. “Cutting the foam is a little tricky; you have to practice at it. But a sharp knife is important. Usually after six or seven big cuts, you have to sharpen your knife again.”
- Martens uses a steel yardstick for measurements and for a straight edge cutting brace.
- While the snap-together foam tiles are conveniently available, Martens is working on sourcing large rolls of the material. Working in bulk, he said, would eliminate the interlocking edges inherent to foam flooring tiles.
“I start by cutting off those little puzzle pieces, but if you can find the foam in large rolls you won’t have to cut off those pieces,” he said.
- Always place a dummy piece of foam below the one you’re cutting to fit. Two benefits: First, you can cut with confidence that you won’t damage boat carpet or any other surface on which you’re working. Moreover, you won’t dull your blade when it breaks through and makes contact with the underlying surface.